allmineral to refine Spanish ore to world market standard
For the construction of its new processing plant in La Parrilla, W Resources is banking on the Duisburg technology leader three times over.
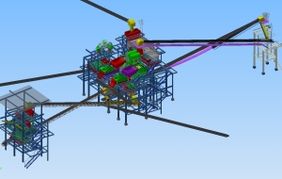
The Spanish tungsten and tin mine at La Parrilla is banking on state-of-the-art processing technology from allmineral to achieve its ambitious extraction targets. The Duisburg-based systems specialist was once again contracted by the mine operators in January 2018 after it had successfully completed the execution planning and construction of the ‘pre-concentrator’ using two alljig® jigs. A fully customised processing plant to be commissioned on site by allmineral is soon to go online as the last process stage in the tungsten ore enrichment.
The La Parrilla mine close to the Portuguese border is one of five sites on the Iberian peninsula mined for mineral raw materials by W Resources (WRES). In the years to come the two alljig® fines jigs and the adjoining processing plant will help double annual output in the Extremadura region to 5,000 tonnes a year, without compromising on the competitive product quality, which is world market standard.
Thanks to the innovative processing technology the mine operators are confident of achieving a metal recovery of at least 90% from the dressed ore minerals. The emphasis is on scheelite, a tungsten mineral that can be enriched through gravimetric grading, then enriched into concentrates with a tungsten content in excess of 66%. The La Parrilla mine also extracts cassiterite, the world’s most important tin ore, with a theoretical tin content of 78.8%.
With a throughput of 350 tonnes per hour the two alljig® jigs will provide reliable and adaptable grading, enrichment and cleaning of the pre-ground ore. The air-pulsed, resource-friendly twin jigs remain physically stable during operation, a precondition for an optimum jigging stroke with minimised energy consumption. With the alljig® process the feed material is initially fluidised with pulsed water, with the grains graded according to density. The jigs separate the specifically lighter scheelite-poor yield from the specifically heavier scheelite-rich ore from the stratified material bed. The jigging motion used to separate the grains does not cause any wear and tear and is induced by adding air so the stroke movement (frequency, amplitude and waveform) can be adjusted across a broad range of operating parameters.
The Concentration Project was only commissioned by W Resources as recently as January 2018. allmineral is to install it as the third core component of the plant infrastructure and then adapt and commission it on site along with all the auxiliary units.
The processing plant with a capacity of 155 tonnes per hour connected to the pre-concentration stage through the alljig® jigs will ensure that the tailings are separated from the valuable material, thereby achieving a 65% WO3 recovery.
The fines produced in several processing stages are to be recovered in a separate circuit.
For Michael Masterman, chairman of W Resources, commissioning allmineral with the Concentrator Project is both a milestone and a mainstay in La Parilla’s development and financing programme. All the key plant components are now contractually bound and aligned with the USD 30 m credit financing. allmineral is responsible for planning, building and supplying the main machine units, facilitating and expediting the timely completion of the plant as a whole within the stipulated cost framework.
allmineral gratefully acknowledges the trust placed in its services by the customer and looks forward to the collaboration with W Resources.
For more information:
allmineral
Aufbereitungstechnik GmbH & Co. KG
Baumstrasse 45
47198 Duisburg | Germany
Phone: +49 (0)2066-9917-0
Fax: +49 (0)2066 -9917-17
e-mail: head@1751752602allmi1751752602neral1751752602.com1751752602
www.allmineral.com